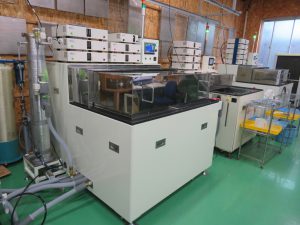
相模原市内の本社に増設した自社製装置
Blue Star R.D. (1 Yokoyamadai, Chuo-ku, Sagamihara City), a developer and manufacturer of ultrasonic deburring and cleaning equipment, installed its own ultrasonic deburring equipment at its headquarters in Sagamihara City in April and began full-scale deburring The company has been engaged in the deburring business on a contract basis. The company is the first company in Japan to commercialize only deburring (according to the company). On April 15, the company opened a business base in Okazaki City, Aichi Prefecture, where many of its customers are located, by installing a large piece of equipment. The company received a business restructuring subsidy from the Small and Medium Enterprise Agency, which it used to expand its contract cleaning equipment. [May 1, 2022 issue
The idea behind the full-fledged launch of the outsourced contracting business is to approach potential customers who are not ready to install deburring washers and other equipment. In the past, the company has only undertaken processing work on a trial basis or as a stopgap measure until the equipment is delivered. Against a backdrop of labor shortages and soaring material unit costs, manufacturers have been reluctant to invest in equipment, and opportunities to actually see deburring performed have been decreasing due to the impact of a new type of infectious disease.
In recent years, automotive parts have been shifting from heavy metals to lightweight resins (plastics) in order to achieve lower fuel consumption due to increased awareness of environmental protection. In particular, “inquiries from companies that use PPS (polyphenylene sulfide), a high-performance plastic, have been increasing, and the properties of the material (which does not lose its hardness even at high temperatures) make it ideal for ultrasonic deburring,” says Yoshihide Shibano, chairman of the company. (Chairman Yoshihide Shibano).
The area around Okazaki City, where the new Chubu Ultrasonic Deburring Center will be located, has many customers, including Toyota Industries Corporation (Kariya City), to which the company supplied products when it was founded, as well as Toyota Motor Corporation (Toyota City) and manufacturers of parts used in Toyota-made vehicles. The company receives orders mainly from companies that handle metal parts, but it is expanding its customer base to include plastic products and electronic and semiconductor parts due to the electrification of automobiles.
The company has installed ultrasonic deburring and cleaning equipment in its laboratory at its headquarters in Sagamihara City and at its center in Okazaki City. In addition, the head office has installed a “vacuum pretreatment type” that creates a vacuum in the cleaning tank to remove all air attached to the object to be cleaned, and a cleaning system that uses a hydrocarbon-based solution.
This technology, in which the company excels, uses sound waves with a high frequency that is inaudible to the human ear to generate microscopic bubbles, and the impact of the bubbles popping removes burrs (unwanted protrusions on the work surface). The system is applicable to a wide variety of materials, including metals, resins, ceramics, and composite materials. In some cases, burrs are removed manually after processing, and this has been one of the reasons for relocating manufacturing bases to foreign countries where labor costs are relatively low.
Ultrasonic deburring and cleaning is recommended as a way for local manufacturers to reduce labor costs, stabilize quality, and strengthen international competitiveness. Chairman Shibano is optimistic, saying, “It will take time for the deburring business to get off the ground, but we believe it will enhance the reliability of our equipment, promote sales, and provide a stable revenue stream.
Translated with www.DeepL.com/Translator (free version)