大和市中央林間に営業・製造拠点を置き、3D(3次元)プリンターを使った製造受注などを手掛ける「SOLIZE(ソライズ)」(東京都千代田区)は、飯田ピアノ=静岡県三島市)が「KuraDA(クラダ)」のブランドで展開する新作ヘッドホン「KD―Q1」のハウジング(内部を保護する覆い)やカバーなどの部品を3Dプリンターで製造する。従来の成形方法では不可能とされる理想的な形状と重量を実現し、装着性と高音質を両立した。【2024年8月1日号掲載】
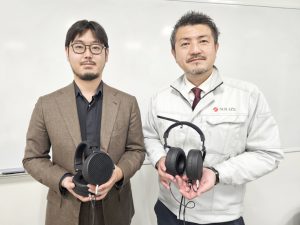
クラダの飯田代表㊧とソライズの太田部長
♪音響に理想的な素材
同ブランドの従来モデルでは、ハウジングに木材やジュラルミンなどの素材を用い、切削加工による製造を行ってきた。切削加工は高精度な加工が可能だが、複雑な形状な製品の量産が難しい上に、切りくずが発生するなど材料効率が悪く、高コストとなる点が悩みだった。
クラダの飯田良平代表は、3Dプリントの導入に踏み込んだ理由について「切削加工ではこだわると重量がかさむ。金属の中では軽量なアルミでも限界があり、重量が増すと側圧(頭を挟む力)も増し快適性に影響が出る」と説明。軽いヘッドホンを作りたかったというが、「金型を作るには高コスト。ハイエンドで少量生産のヘッドホン作りには効果が見込めなかった」と明かした。
関心を持ったのは、3Dプリントでのものづくりが一般化した7~8年前だった。オンデマンドの出力サービスを利用し、金属製の旧モデルをそのまま樹脂で試作。飯田代表は「強度や制度の面で高いレベルでクリアできることが分かった」と話す。
3Dプリントはデザインが自由で、複雑な形状を一度の出力で造形できる点がメリット。材料の粉末樹脂に黒いインクで形状を描き、熱を加えて層を形成していく「粉末焼結」という方式で、従来の10倍の速度で、複雑な形状の部品18台分を高精度に製造できる点が特徴。耐候性に優れたPA(ポリエアミド)12樹脂に40%のガラスビーズを混合した素材を使うことで、曲げに対する弾性や引っ張り強度、熱変形温度など高い機械的強度を実現している。
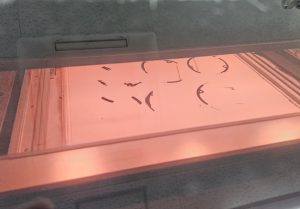
ヘッドホンの本体部品を製造する粉末造形プリンtナー
3Dプリントで製造するのは、ヘッドホンの音質を左右するため剛性が必要とされるカバー、ハウジング、ケース、ブラケット。「内部損失が非常に高くありながら、密度が低いので軽く、オーディオ的に理想的な素材である。金属で製造したハウジングに比べて、振動の収まりがいい」(飯田代表)とする。
♪3Dプリントで先駆
ソライズは1990年から光造形による試作品制作を手掛ける3D造形の先駆的存在で、今回の製造に使用する粉末造形機5台のほか、ハイエンド機35台を保有。レクサス・LC500のオイルクーラーダクトに、ソライズが3Dプリントで量産するパーツが採用されるなど技術力が高く評価されている。
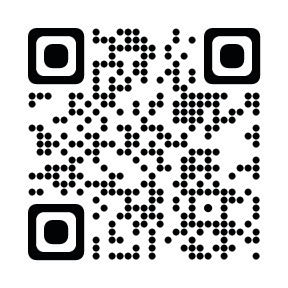
3Dプリンターの実働動画=YOUTUBEショート動画
「安定してモノをつくる品質管理の手法にもあわせて取り組んでいる」と話すソライズの太田亨部長は、ヘッドホン開発ノウハウを自動車分野にどうフィードバックできるかという問いに「3Dプリンターでしかできない形状を造形することで、内装の質感の向上や静穏性が良くなるといった要素が増えていくのでは」と可能性に期待した。
クラダが開発・製造するヘッドホンは、「日本の産業を盛り上げたい」「日本の高い技術力を活用したい」との観点で、すべて日本国内で製された部品を使う。粉末造形が生む風合いを生かしながら、仕上げ塗装には「真鍮ブラシで擦っても傷がつかない」という高耐久塗料を浜松市のメーカーから調達する。
同社は13年に木製ハウジングのモデル、14年に2片の木材を組み合わせたモデルなど計3種を開発・販売。今回の新モデルは最後に発売したモデル「KD―P1」の生産終了から6年となる。
KD―Q1(市場想定価格20万円)はすでに予約を開始しており、8月5日から全国のオーディオ専門店や家電量販店で販売される。9月からは三島市のふるさと納税返礼品にも加わる見込み。